Most of the traditional thread processing methods use taps to tap threads. Nowadays, with the advancement of technology, thread milling processing gradually replaces tap processing.
Traditional tapping thread processing method
Taps are tools used to process medium and small-sized internal threads. They have grooves along the axial direction. It has the characteristics of simple structure and easy use, and can be operated manually or used on machine tools. Classification of taps:
According to the shape, they can be divided into three categories: straight flute taps, spiral flute taps and spiral tip taps.
Straight flute tap: The structure is simple, the blade inclination angle is zero, the cutting layer area of each cutting tooth increases stepwise, and the grooves are arranged straightly. The cutting edge has good strength, is easy to grind, has large cutting torque during processing, and has poor chip breaking and chip removal capabilities. The biggest feature is that it has the strongest versatility. It can be processed whether it is through holes or non-through holes, non-ferrous metals or ferrous metals, and the price is the cheapest.
Spiral flute tap: named after its chip flutes are arranged in a spiral shape. Spiral flute taps are divided into left-hand spiral flute taps and right-hand spiral flute taps. The chip flutes of spiral fluted taps are spiral and can be divided into left-handed and right-handed according to the direction of rotation. When tapping with a left-hand spiral flute tap, the chips are discharged downward, which is suitable for through holes; when tapping with a right-hand spiral flute tap, the chips are discharged upward, which is suitable for blind holes. This kind of tap has a longer service life and faster cutting speed, which is 30% to 50% higher than that of straight flute taps. It can process threads with the highest precision.
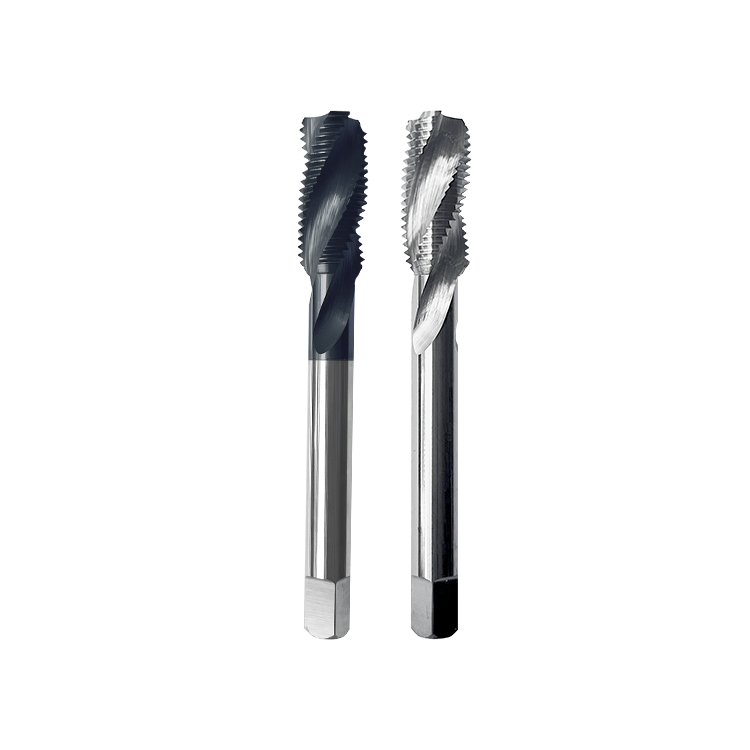
Spiral point tap: also known as tip tap, suitable for through holes and deep threads, with high strength, long life, fast cutting speed, stable dimensions, and clear tooth lines (especially fine teeth). For more CNC programming knowledge, follow the WeChat official account (CNC programming teaching), it is a deformation of a straight flute tap. The cutting edge has an inclined groove on one side of the straight flute, forming an angle, and the chips are discharged forward in the direction of the feed. Suitable for through-hole processing and high-precision threads. Commonly used for processing non-ferrous metals, stainless steel and ferrous metals.
For small-sized internal threads, thread tapping is almost the only processing technology available. However, this process is difficult to process. Since the tap is almost buried in the workpiece for cutting, the processing load per tooth is greater than that of other tools, and the contact surface between the tap and the workpiece along the thread is very large.
Modern methods of thread milling
Thread milling is a processing method that uses the three-axis linkage of CNC machine tools to use the rotation of the milling cutter as the main motion to generate the thread diameter; while the workpiece makes feed motion to generate the thread pitch.
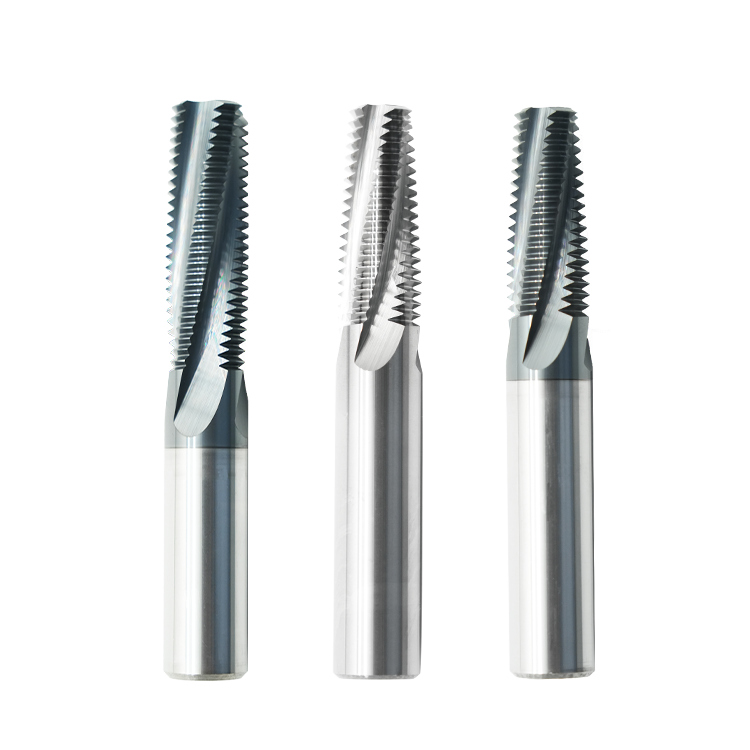
Advantages of thread milling:
1. It has high processing efficiency, surface quality and dimensional accuracy.
2. Good stability, safe and reliable, with wider and more flexible usage methods and application occasions.
Limitations of thread milling:
1. A three-axis linkage CNC machine tool is required.
2. Programming is also troublesome, and mass production is still relatively common, so the single production cost is not cost-effective.
Although the traditional tapping thread processing method has low precision and easy tool wear, it is highly practical; the modern thread milling method has high surface quality and precision, but the processing cost is expensive and CNC programming is cumbersome. In actual production and processing, the most reasonable choice should be made from multiple aspects such as craftsmanship, usability and economy.
In addition to choosing a suitable processing industry, you also need to choose a high-performance environmentally friendly cutting fluid for cooperating processing.
Selection of thread cutting fluid:
When cutting threads, the tool is in wedge-shaped contact with the cutting material. Three sides of the cutting edge are surrounded by the cutting material. It is difficult to remove chips due to large cutting torque. Heat cannot be taken away by the cutting in time. The tool is prone to wear, cutting debris is crowded and prone to vibration. Especially when threading and tapping, the cutting conditions are more demanding, and chipping and broken taps sometimes occur. The cutting fluid is required to have both a lower friction coefficient and a higher extreme pressure to reduce the frictional resistance of the tool and extend the service life of the tool. , generally the compound cutting fluid SCC760 containing both oily agent and extreme pressure agent should be used.
In addition, the permeability of the cutting fluid is very important when tapping threads. Whether the cutting fluid can penetrate into the blade in time has a great impact on the durability of the tap. The permeability of the cutting fluid is related to the viscosity. Oils with lower viscosity have better permeability. SCC618 cutting fluid. When tapping a blind hole, it is difficult for the cutting fluid to enter the hole. In this case, it is better to use a cutting fluid with high viscosity and strong adhesion, such as tapping oil NC300. To sum up, when choosing cutting fluid, it is related to the material of the product, machining process, equipment, etc. Choose the appropriate cutting fluid based on various factors.