1. Pour some lubricating oil, use a sharp hairpin or chopper to slowly knock out the fracture surface in the opposite direction, and occasionally turn the iron over to sharpen it (the most common method in the workshop, but for threaded holes with too small diameter or broken taps that are too large) It may not be suitable if it is too long, but you can try).
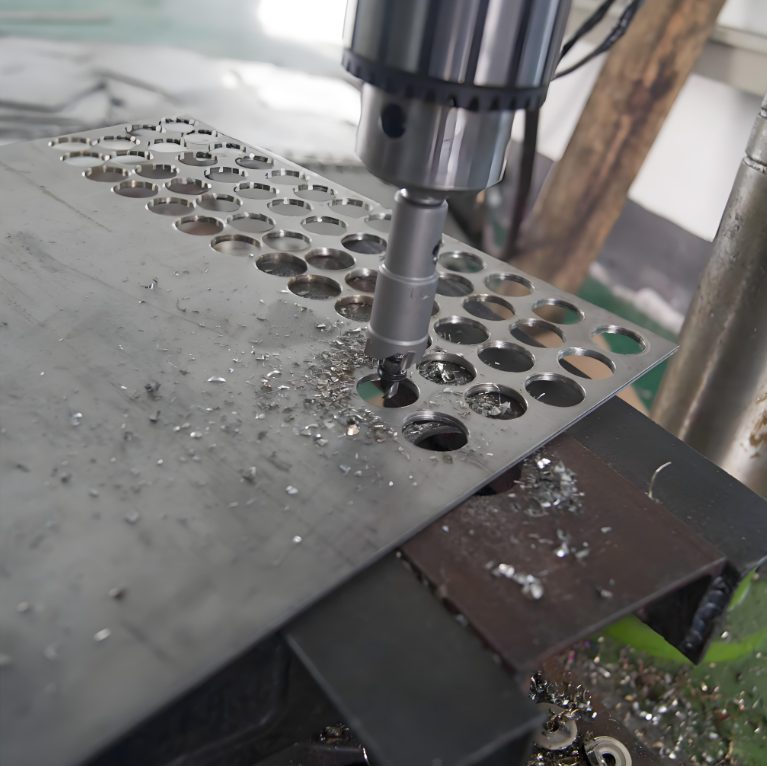
2. Weld a handle or hexagonal nut on the broken section of the tap, and then gently turn it out (this is a good method, but welding is a bit troublesome, and if it is the same, it is not suitable for taps with smaller diameters)
3. Use a special tool: the broken tap extractor. The principle is that the workpiece and the tap are connected to the positive and negative electrodes respectively, and the electrolyte is filled in the middle, causing the workpiece to discharge and corrode the tap, and then assisted to remove it with needle-nose pliers, which will cause little damage to the inner hole;
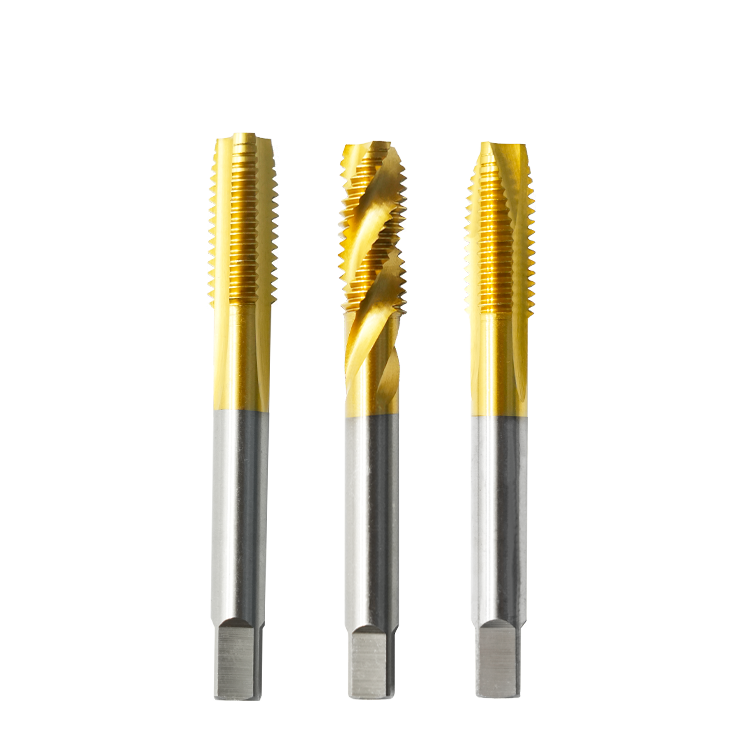
4. Hold the steel roller against the crack of the tap and slowly tap it with a small hammer. The tap is relatively brittle and will eventually break into slag. Or, even simpler, just drill and boring the threaded hole of the broken tap and re-expand and tap (method) It's a bit barbaric. If the diameter of the tap is too small, it will be difficult to use. If the diameter is too large, it will be quite tiring to tap);
5. Weld the threaded hole where the broken tap is located flat, grind it flat, and re-drill it. Although it is difficult, you can drill it in slowly (if the threaded hole can be repositioned, it is recommended to change it when re-drilling and tapping. to the side of the original threaded hole);
6. Drill a slot into the cross section of the broken tap and twist it in the opposite direction with a screwdriver (it is difficult to cut out the slot, especially if the diameter of the tap is small);
7. Drill the threaded hole of the broken tap into a larger size, then insert a wire thread sleeve or pin or something, then weld, grind, and drill and tap again. You can basically achieve the same result (this method is troublesome, but it is very practical. , the size of the tap does not matter);
8. Use electric pulse to remove it, electric spark or wire cutting can be used. If the hole is damaged, you can enlarge the hole and add a wire thread insert (this method is simpler and more convenient. As for the coaxiality, don’t consider it for the time being, unless your threaded hole is the same. Axiality directly affects the quality of the equipment);
9. Make a simple tool and insert it into the chip groove of the broken tap section at the same time, and carefully pull it out in the opposite direction. For example, you can use a broken tap with a square tenon to screw 2 nuts on it, and use steel wire (the number is the same as the number of grooves of the tap) ) into the empty slot of the broken tap and nut, and then use the hinge lever to pull the square tenon in the exit direction to take out the broken tap (the main idea of this method is to open the chip removal groove of the broken tap, using steel wire, preferably Use a steel needle to make a special wrench for removing broken wires. Of course, if such broken wires often occur in the workshop, it is better to make a tool wrench like this);
10. Nitric acid solution can corrode high-speed steel taps without scrapping the workpiece;
11. Use an acetylene flame or a blowtorch to anneal the tap, and then use a drill bit to drill. At this time, the diameter of the drill bit should be smaller than the diameter of the bottom hole. The drill hole should also be aligned with the center to prevent the thread from being drilled. After the hole is drilled, drive a flat shape. Or use a square punch and use a wrench to unscrew the tap;
12. Use the pneumatic drill to reverse the direction and take it out. It all depends on the feel of the hand, because the tap is not drilled out directly, but the tap is rotated out with slow speed and a little friction (similar to the half clutch of a car);
13. You can use a grinder to smooth the broken wire, then use a small drill bit to drill first, and then gradually use a larger drill bit. The broken wire will gradually fall off. After falling off, use a tap of the original size to tap the tooth again, like this The advantage is that there is no need to increase the aperture;
14. Weld an iron rod to the broken object and unscrew it. (Disadvantages: too small broken objects cannot be welded; extremely high welding skills are required, and the workpiece is easily burned; the welding joint is easy to break, and the chance of being able to remove the broken objects is very small)
15. Use a tapered tool that is harder than the broken object to pry. (Disadvantages: It is only suitable for brittle broken objects. Crush the broken objects and then slowly pick them out; the broken objects are too deep and too small to be removed; it is easy to damage the original holes)
16. Make a hexagonal electrode smaller than the diameter of the inserted object, use an EDM machine to machine a hexagonal counterbore on the inserted object, and then use an internal hexagonal wrench to unscrew it. (Disadvantages: useless for rusty or stuck break-in objects; useless for large workpieces; useless for break-in objects that are too small; time-consuming and troublesome)
17. Directly use an electrode smaller than the object to be cut, and use an EDM machine to punch. (Disadvantages: Useless for large workpieces and cannot be placed on the EDM machine table; time consuming; carbon will easily accumulate if it is too deep and cannot be drilled)
18. Use an alloy drill bit (disadvantages: easy to damage the original hole; useless for hard cutting objects; alloy drill bits are brittle and easy to break)
19. There is now a portable machine tool designed and manufactured using the principle of electrical machining, which can easily and quickly remove broken screws and tap drill bits.
20. If the screw is not too hard, you can flatten the end face, then find the center point, use a sample punch to punch a small point up, use a smaller drill bit to drill first, make sure it is vertical, and then use a broken wire extractor to twist it in the opposite direction. Just go out.
21. If you can't buy a broken wire extractor, use a larger drill bit to continue to expand the hole. When the hole diameter is close to the screw, some wires will fall off due to force. Just remove the remaining wire threads and then use a tap to reshape the hole.
22. If the broken screw wire is exposed, or the broken screw is not strict, you can still use a hand saw to cut it. You can cut the slits and even the outer casing, and then remove it with a flat-blade screwdriver.
23. If the broken wire is exposed to a certain length, and the melting point of the mechanical material is not too low, you can use electric welding to weld an extended T-shaped rod on the screw, so that it can be easily screwed out from the welded rod.
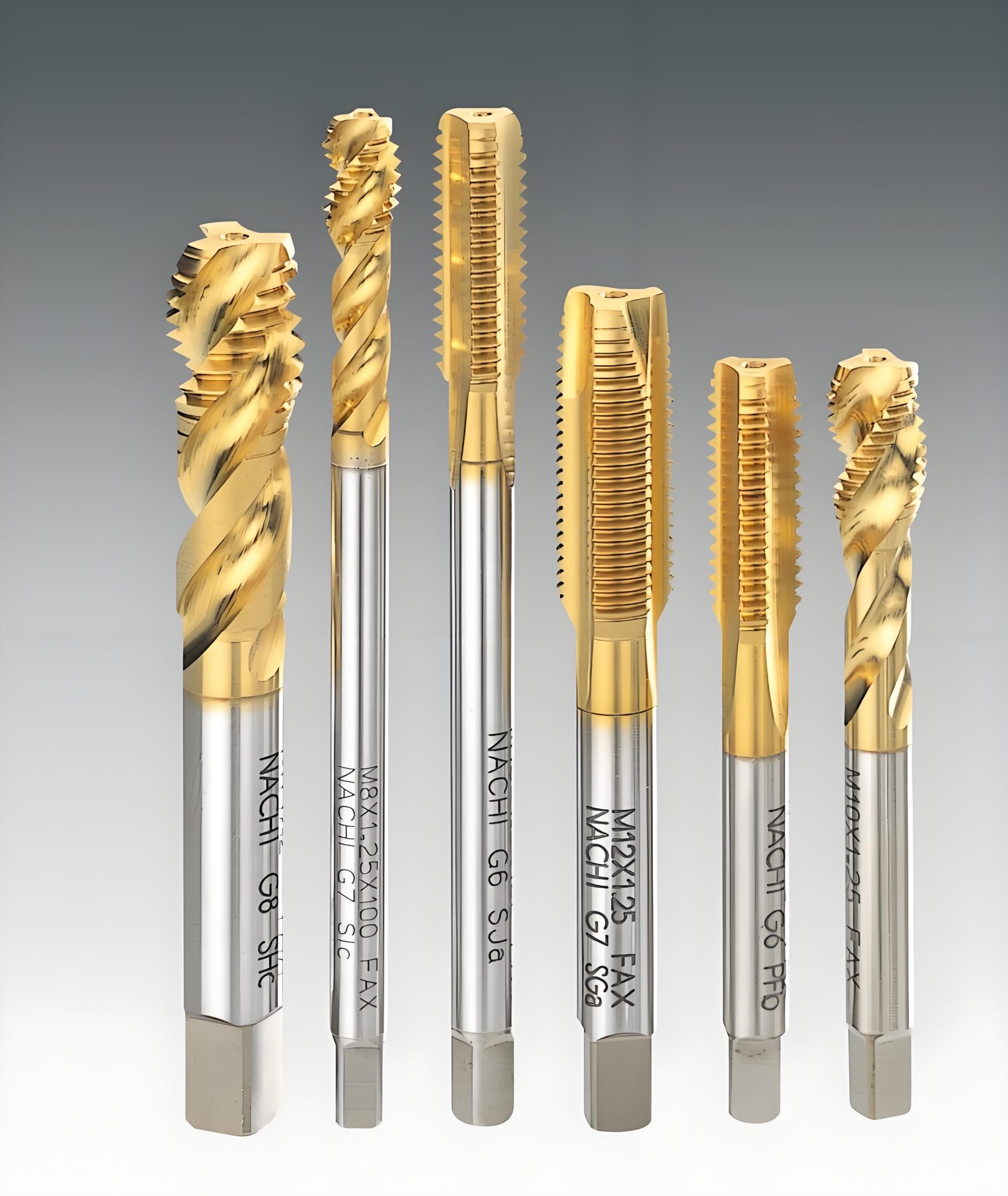
24. If the screws are severely rusted and cannot be treated with the above method, it is recommended to roast them red and then add a little lubricating oil, and then use the above corresponding methods to deal with them.
25. After a lot of hard work, although the screws were taken out, the holes were useless at this time, so I simply drilled a larger hole and tapped it. If the original screw position and size are limited, you can also drill a larger hole. Screw it in, or tap it directly by welding it, and then drill a small hole in the center of the big screw and tap it. However, it is sometimes difficult to tap the internal metal structure after welding.