1. Chip discharge mode:

Straight flute taps: The cutting edge is straight and has no helical rise angle, so the chips generated during the tapping process are discharged in a straight direction, usually suitable for through-hole thread processing. Since the chips are discharged directly downwards, for long through holes and continuous production, poor chip removal may lead to chip accumulation or damage to the threads already machined.
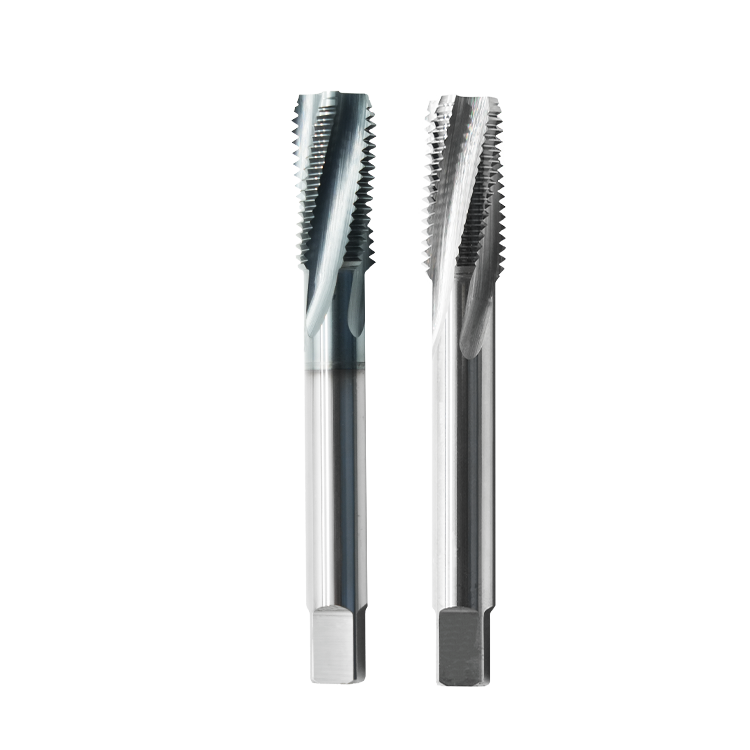
Spiral flute taps (including right-hand and left-hand): The chipformer is spiral with a clear helical rise. When tapping with right-hand spiral flute taps, chips are pushed upward by the spiral groove, which is suitable for blind hole machining and can effectively avoid chip blockage and discharge chips out of the hole; left-hand spiral flute taps, on the contrary, are more suitable for through-hole for some special applications due to the downward chip characteristics.
2. Scope of application:
Straight flute taps: due to its simple structure, low manufacturing costs, and the accuracy requirements are not particularly high in the common thread processing is more common, especially for non-ferrous metals or other soft materials, fast tapping, and the thread depth of shallow holes have limitations.
Spiral flute taps: more complex design, relatively high cost, but with better chip removal performance and stability, suitable for hardness of metal materials, deep blind holes and powder chips are not easy to discharge conditions, tapping accuracy is relatively higher, but also reduces the risk of tool breakage.
3. Machining effect and efficiency:
Straight groove taps: large contact area during tapping, greater feed resistance, slower tapping speed, and due to the problem of chip removal, not suitable for blind hole processing, otherwise it is easy to cause chip blockage and damage to the thread quality.
Spiral groove taps: Due to the design of spiral groove, it reduces the friction resistance during the tapping process, improves the cutting efficiency and thread surface quality, and also reduces the wear of taps.