Spiral taps and straight flute taps are two common thread processing tools, each with different characteristics and applicable scenarios.
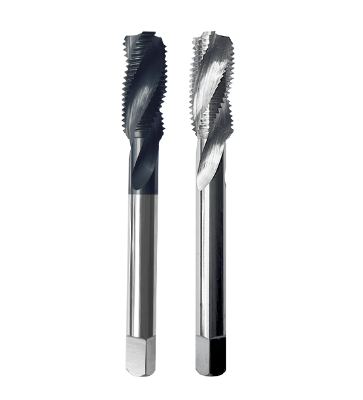
Spiral Tap features:
1. Suitable for processing blind hole threads, chips are discharged backward, which helps to improve chip removal efficiency.
2. The selection of the helix angle depends on the material characteristics. For example, when processing ferrous metals, the helix angle should be smaller, about 30 degrees, to ensure the strength of the spiral teeth; when processing non-ferrous metals, the helix angle should be larger. About 45 degrees to provide sharper cutting.
3. The actual cutting rake angle of the spiral flute tap will increase as the helix angle increases, which helps to improve cutting efficiency.
4. Longer service life, which can be increased by 30% to 50% compared with ordinary straight groove taps, and some can be as high as 2 times more.
5. Tapping efficiency is high and cost is low, because the chips are easy to discharge, reducing chip blocking and improving production efficiency.
6. The cooling and lubrication conditions are good, because the metal chips can be automatically discharged along the spiral groove and are not easily blocked, which improves the cooling and lubrication conditions during cutting.
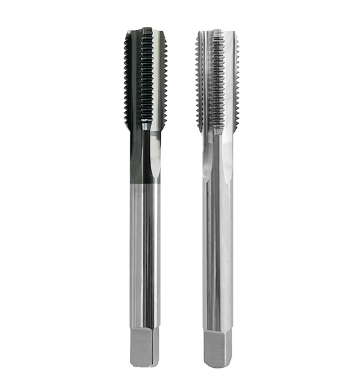
Straight Tap features:
1. The most versatile, it can be used for processing through holes or blind holes, non-ferrous metals or ferrous metals.
2. The price is relatively cheap, but it is poorly targeted and is not specifically designed for a certain type of material.
3. The cutting cone part can have different numbers of teeth. The short cone is suitable for closed holes, and the long cone is suitable for through holes.
4. When the bottom hole is deep enough, you should try to use a tap with a longer cutting cone, which can share more cutting load and extend the service life.
When selecting a tap, you need to consider factors such as the thread type (through hole or blind hole), material and hardness, thread depth and accuracy requirements. Spiral taps are particularly suitable for blind hole processing, while straight flute taps are suitable for a variety of general applications.