Pre-Grinding Inspection of the Grinding Wheel
Before starting the sharpening process, it is crucial to inspect the grinding wheel. If any of the following conditions are detected—wheel runout, irregular cylindrical surface, or excessively large radius on the edges—correction is necessary. This can be achieved using a grinding wheel dresser (such as a diamond dresser or a toothed dresser) to true the cylindrical surface of the wheel. Alternatively, an old grinding wheel with relatively harder abrasive particles can also be used for this purpose. If the side face of the grinding wheel is no longer flat, it is advisable to replace the wheel.
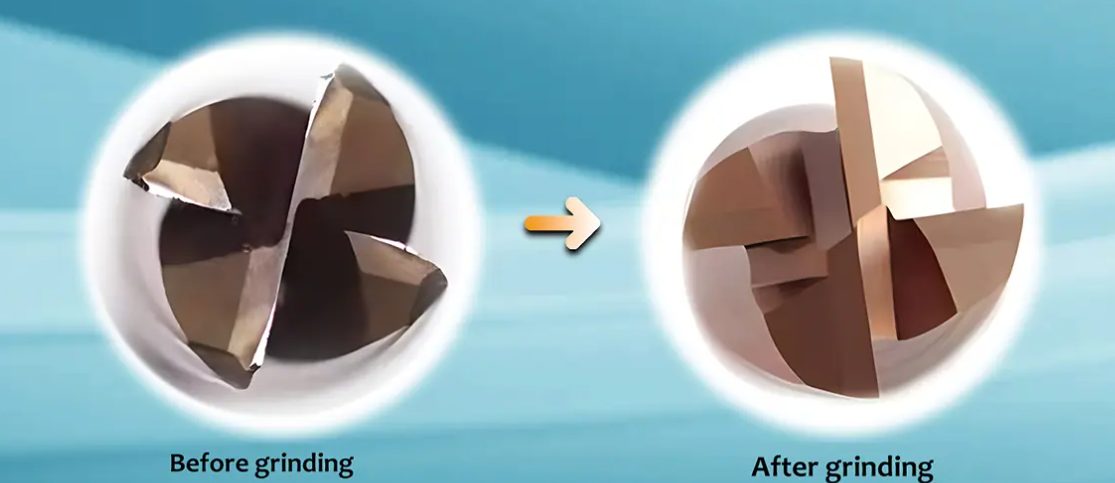
Techniques for Grinding the End Faces of End Mills
1. Grinding the End Faces of End Mills Flat
Regardless of the number of cutting edges, the first step is to grind the end face of the end mill flat and perpendicular to the tool axis. This is essential to ensure that the highest points of all cutting edges are in the same plane. Here are several methods to check and correct the perpendicularity of the end face relative to the tool axis:
a. Visual Inspection
Place the end mill, with its cutting edges facing downward, on a flat surface and observe the tilt angle from left to right. Rotate the end mill 180° and repeat the observation. If the tilt angles observed in the same direction are different, grinding is required until the tilt angles are consistent in the same direction. Then, rotate the end mill 90° and repeat the process.
b. Using a Square
On a flat surface, use a 90° square to check the end mill. Place both the end mill and the square flat and observe whether there are any gaps between the end mill and the square, or whether the gaps are uniform. Based on the gaps, determine the perpendicularity of the end mill and grind accordingly.
c. Self-Correction
Mount the end mill in a drill press or milling machine chuck, with an old grinding wheel segment placed below. Select an appropriate spindle speed, start the machine, and lower the end mill to grind on the wheel segment. Adjust the grinding process based on the condition of the end face after grinding.
2. Creating a Cross-Coolant Groove on the End Face of End Mills
If a four-flute end mill does not have a circular groove at the front of its end face, it is necessary to use the radius of the grinding wheel to create a cross groove along the direction of the helical flute, with a depth of approximately 1–2 mm (too deep can cause chipping, while too shallow makes it difficult to grind the secondary clearance angle). When creating the groove, ensure that the side of the grinding wheel does not contact the adjacent cutting edge (Note: This cross groove serves to discharge chips. If not created, the rake angle of the inwardly inclined cutting edge should be increased).
3. Grinding the Cutting Edges on the End Face of End Mills
When grinding each cutting edge:
a. Use the tip of each cutting edge as the reference point, and retain the tip while grinding the primary rake angle (if there is no chipping, this can be skipped), primary clearance angle, secondary clearance angle (for heavy cutting, it is recommended to increase the wedge angle on the front of the tool to enhance strength), and cutting edge inclination.
b. The recommended angles are as follows: primary clearance angle of 6°–8°, secondary clearance angle of 30°–45°, and cutting edge inclination of 1°–3°. The primary clearance angle should be adjusted based on the hardness of the workpiece material; harder materials require a smaller angle. The cutting edge inclination should be such that all four edges are concave towards the center. A flatter inclination angle results in better surface roughness. When the cutting depth is deeper (e.g., greater than 2 mm but within the allowable range), the surface roughness actually improves because the entire cutting edge is engaged in cutting.
c. After grinding, stand the end mill upright on a flat surface. If the axis is vertical, all cutting tips should be aligned, and the angles of the cutting edges should be uniformly centered, indicating that the grinding meets the requirements.
Similarly, a 90° square can be used on a flat surface to check for gaps or uniformity of gaps between the end mill and the square. Start by observing the two relatively higher feet (the ones that touch the surface first). If they are not vertical, grind the higher feet until they are level with the opposite feet (i.e., vertical). At this point, a difference in height will appear between these two feet and the other two opposite feet, causing the end mill to wobble. Then, grind down the two higher feet simultaneously. Rotate the end mill 90° and check the verticality of the other two opposite feet. Ultimately, all four feet should touch the surface simultaneously, and the end mill should be vertical.
During manual grinding, it is challenging to control the height of the cutting edges and the various angles. When training, it is important to adapt to individual skills, focusing on grinding a slight clearance angle. If the top cutting edge is uneven, simply ensure that the highest point is the tip. Additionally, unless the end mill is used for corner cleaning in internal cavities, a chamfer greater than 0.2 mm can be ground at the tip to enhance its strength.
4. Grinding the Primary Flutes (Side Cutting Edges) of End Mills
If the primary flutes of an end mill are worn, they need to be ground along the helical line on a grinding wheel (a smaller diameter wheel is preferable). This is challenging for beginners. However, after grinding, there will generally be a taper. The smaller the taper, the higher the skill level demonstrated.