Coating is a technology that applies one or more thin films to the surface of a milling cutter to improve the performance and life of the milling cutter. Common coating materials include titanium, titanium nitride, titanium carbide, etc. The coating process usually uses physical vapor deposition (PVD) or chemical vapor deposition (CVD) methods.Compared with the milling cutter material itself, the hard material coating has higher hardness and stronger wear resistance.
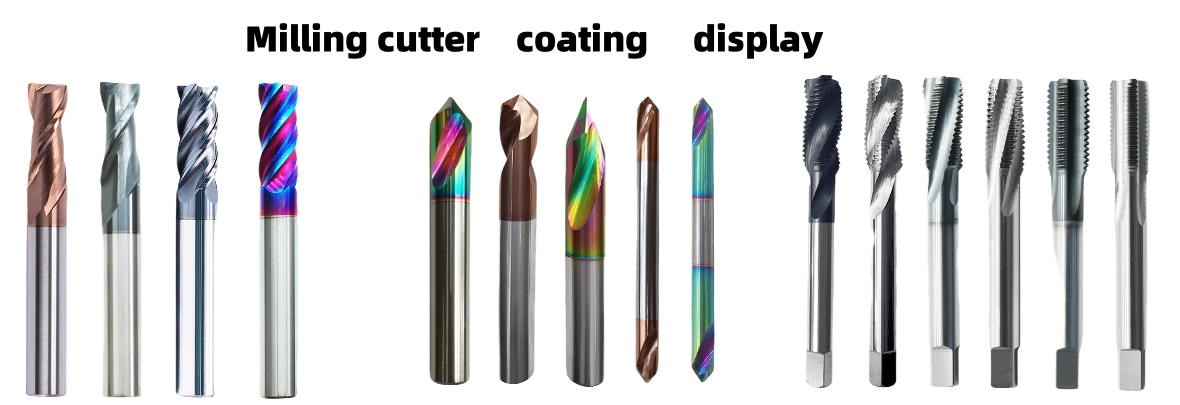
Below are some common coating methods and their respective characteristics:
Surface treatment/Coating | Method/Coating | Features |
Uncoated | No processing | / |
Steam treatment | Steam treatment | High speed steel steam treatment |
Blade steam treatment | Steam treatment | High speed steel edge steam treatment |
TiN | TiN coating | Universal coating |
TIP | TN head coating | Special coating for optimal drainage performance |
TFL | Tinal coating | Highly efficient coating for a wide range of applications |
TFT | Tinal TOP coating | Highly efficient coating with extremely small friction coefficient |
TFP | Tinal head coating | Efficient coating, perfect chip evacuation performance |
TML | Tinal micro drill bit coating | Special coating for small drill bits with very low coefficient of friction |
XPL | AICrN coating | Efficient coating for maximum wear resistance |
DPL | double coating | Efficient coating for maximum wear resistance |
DPP | Double coating on head | Efficient coating for maximum wear resistance |
AML | AITiN micro drill bit coating | Special coating for small drill bits with very low coefficient of friction |
AMP | AITIN Micro Drill Head Coating | Special coating for small drill bits with very low coefficient of friction |