Based on the type of machined surface, turning tools can be divided into external turning tools, internal turning tools, and end face turning tools.
1. External Turning Tools
External turning tools are used for external turning, to machine the external cylindrical surface of a part, achieving the required size, geometric tolerance accuracy, and surface quality, as shown in Figure A.
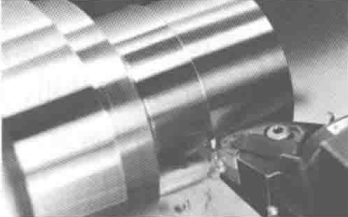
2. Internal Turning Tools
Internal turning tools are used for internal turning, as shown in Figure B. They are used to enlarge the internal hole of a workpiece or machine the inner surface of a hollow workpiece by turning. Most of the machining methods used for external turning can be used to machine internal holes. At this time, the tool is stationary (opposite to the rotation direction of the boring tool in a machining center). When performing external turning, the length of the workpiece and the selected tool holder size generally do not affect the tool overhang, so they can withstand the cutting forces generated during processing. When boring and internal turning, since the hole depth determines the overhang, the hole diameter and length of the part have certain restrictions on the selection of the tool.
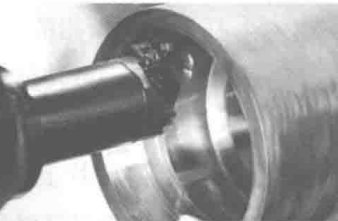
3. End Face Turning Tools
End face turning tools are used for end face turning, as shown in Figure C. The cutting edge is always on a line that intersects with a point on the main shaft axis, resulting in a plane or cone that passes through that point and is perpendicular to the main shaft axis. End face turning tools refer to those tools whose main cutting edge can perform cutting on the end face of the workpiece.
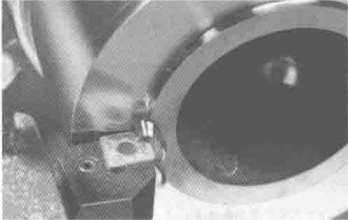