Dovetail End Mills, specialized tools for machining dovetail slots, T-slots, and other unique shapes, are widely used in mold manufacturing, mechanical processing, and other fields. However, with a plethora of products on the market, users often encounter various issues when selecting and using these tools. This article addresses common concerns in detail, helping you master the use of Dovetail End Mills with ease.
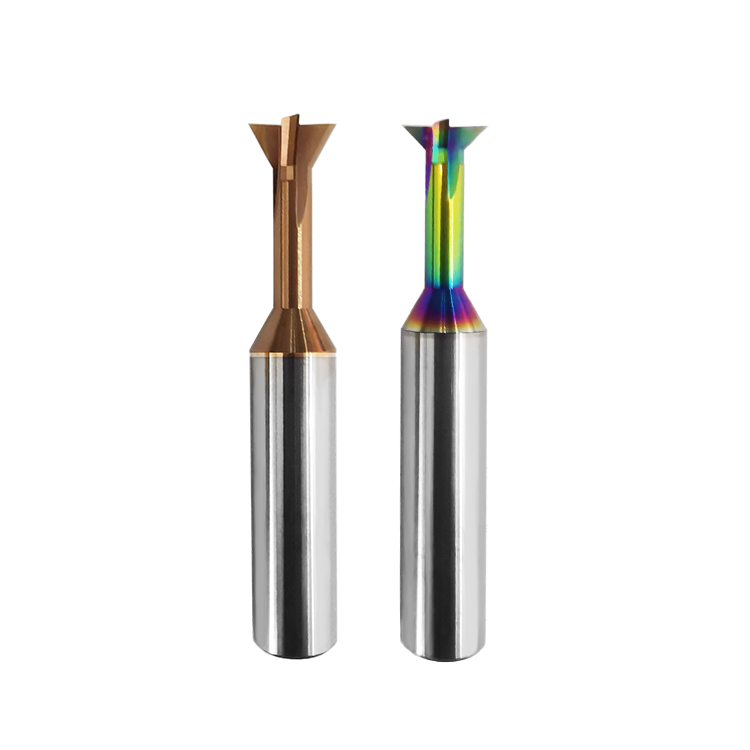
I. Selection Guide
1. How to Choose the Right Dovetail End Mill Angle?
- Common Angles: 45° and 60° are the most common angles, suitable for different machining needs.
- 45°: Ideal for general-strength dovetail slots, such as those in aluminum alloys and mild steels.
- 60°: Suitable for high-strength dovetail slots, such as those in tool steels and stainless steels, providing better support and stability.
- Selection Criteria: Choose based on the hardness and strength of the material being machined, as well as the required strength of the dovetail slot.
2. How to Select the Diameter and Flute Length of a Dovetail End Mill?
- Diameter Selection: Choose a diameter slightly smaller than the width of the dovetail slot.
- Flute Length Selection: Ensure the flute length covers the entire depth of the slot.
3. How Do Coatings Affect the Performance of Dovetail End Mills?
- Common Coatings: TiN, TiCN, and TiAlN coatings enhance the tool's hardness, wear resistance, and heat resistance, extending tool life and improving machining efficiency.
- Selection Advice: Choose coatings based on the material being machined. For example, TiN coatings are suitable for aluminum alloys, while TiAlN coatings are better for stainless steels.
4. How to Evaluate the Quality of a Dovetail End Mill?
- Brand Reputation: Opt for reputable brands to ensure quality.
- Visual Inspection: Check for smooth surfaces and sharp, unchipped cutting edges.
- Material Testing: Use professional equipment to verify the tool's material and hardness.
II. Usage Guide
1. How to Properly Install a Dovetail End Mill?
- Clean the Collet: Ensure the collet is clean before installation to avoid impurities affecting precision.
- Apply Appropriate Clamping Force: Excessive force can deform the tool, while insufficient force can cause it to loosen.
- Check Tool Runout: Use a dial indicator to verify runout after installation, ensuring it is within acceptable limits.
2. How to Set Machining Parameters for a Dovetail End Mill?
- Refer to Manufacturer’s Guidelines: Select cutting speed, feed rate, and depth of cut based on the material and tool diameter.
- Conduct Test Cuts: Perform trial cuts before full-scale machining to adjust parameters as needed.
3. How to Extend the Lifespan of a Dovetail End Mill?
- Use Suitable Coolant: Effectively reduces cutting temperature and minimizes tool wear.
- Avoid Overloading: Choose cutting parameters within the tool's capacity.
- Regularly Inspect Tool Wear: Replace severely worn tools promptly to maintain machining quality.
4. What to Do If a Dovetail End Mill Chips?
- Check Machining Parameters: Ensure feed rate and depth of cut are not excessive.
- Inspect Tool Installation: Verify the tool is securely installed and free of runout.
- Examine Material: Check for hard spots or impurities in the material.
- Replace the Tool: If chipping is severe, replace the tool immediately.
III. Other Questions
1. What Materials Can Dovetail End Mills Machine?
- Suitable for Various Metals: Including aluminum alloys, steels, stainless steels, and tool steels.
- Also Suitable for Some Non-Metals: Such as plastics and wood.
2. What Is the Price Range of Dovetail End Mills?
- Prices Vary by Brand, Specifications, and Coatings: Ranging from a few dollars to several hundred dollars.
- Choose Based on Needs and Budget.
Conclusion
Dovetail End Mills are precision tools that require careful consideration of multiple factors during selection and use. This guide aims to help you address common issues, improve machining efficiency, and achieve better results. If you have further questions, consult the tool manufacturer or a professional technician.